生産最適化(ケーススタディ 3)
注意:このケーススタディは,幾つかの企業のコンサルティングから抽出したもので,特定の企業を想定したものではない.データや登場人物は,架空のものである.
ロジスティックネットワーク設計の結果を,主力の工場長に知らせたところ,繁忙期にはこんなに生産できないとの返事が返ってきた. ロジスティックネットワーク設計モデルでは,年間が需要量が工場の生産能力以下であるという条件で解いていたが, 我社の製品は売れる月とそうでない月があるようだ.さて,どのようなアプローチをとれば良いのであろうか?
月次生産計画の準備
まずは,今まで年ベースで考えていたデータを,工場の生産計画単位である月ベースにすることから始めることにする.
ロジスティックネットワーク設計モデルは,顧客の需要を集約して(クラスタリングして)扱っていた.元データの需要は,各顧客・製品に対する日単位での需要量を保持していたが,これをクラスター単位に集約する.さらに,ロジスティックネットワーク設計で求めた最適なフロー(工場・倉庫,倉庫・顧客間の製品の移動)から,工場(ならびに倉庫)単位での製品の需要量を計算する.
我社の工場は3つあり, 1つは主力工場ですべての製品を作ることができ,他の2つは,約半分の製品だけを作ることが可能である.そのため,製品ごとのサプライ・チェインは,工場(2箇所),倉庫(13箇所),顧客(50箇所)から構成され,2つの工場で役割分担をしている.
さて,主力の工場に割り当てられている倉庫(顧客)の需要量を計算してみる.製品は全部で24種類あり,すべてABCのAカテゴリーなので比較的大きな量になっている.
月別に集約してから製品別に可視化してみよう.
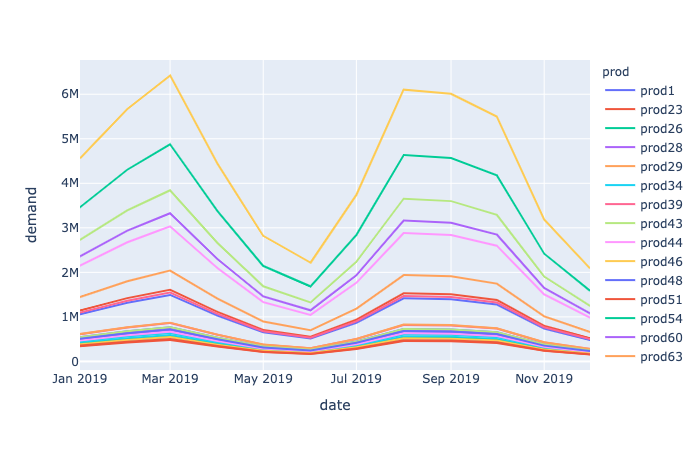
ロットサイズ最適化
生産時間,段取り時間,生産(変動)費用,生産固定(段取り)費用を入れ,ロットサイズ最適化システム OptLot で求解してみる.計算時間は数秒であり,結果は,在庫をうまく使えば生産容量を超えることなしに,すべての需要を満たしている.以下に,各月に生産する製品とその量と在庫の変化の図を示す.
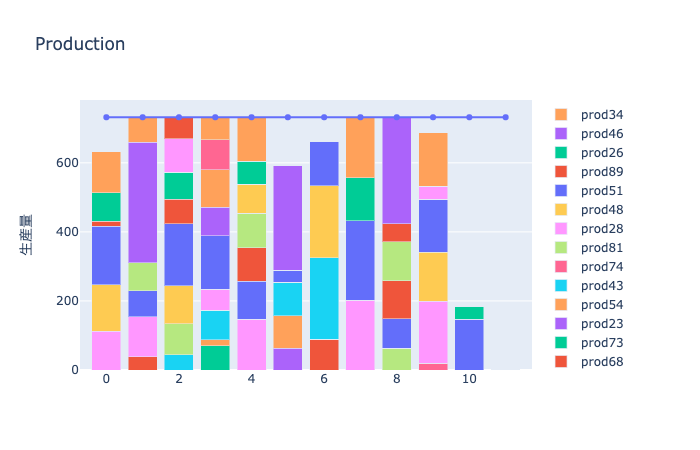
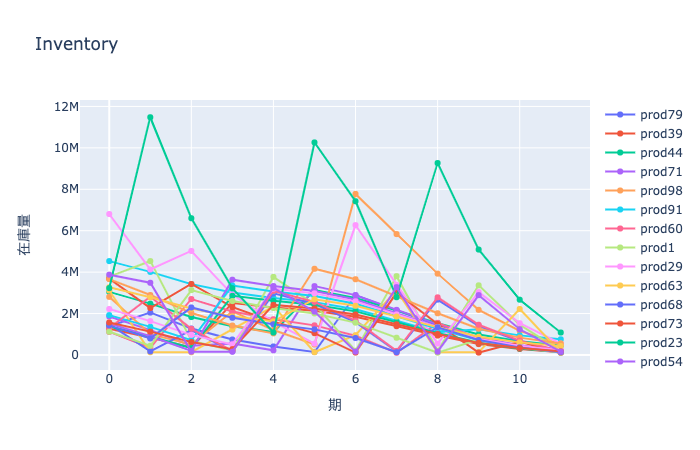
ローリングホライズン方式
上の結果を工場長にプレゼンしたところ,年末にかけて生産量が減少し,在庫も減っていることが指摘された.これは,年度末の在庫量を,工場で指定された安全在庫量に設定したからであるが,実際には少なすぎるようだ.さて,どのようにこの問題点を乗り切れば良いだろうか?
これは,無限期間の動的な問題を,12ヶ月の静的な問題に帰着させたことによる.実際の会社は,12月で閉める訳ではない.解決法としては色々考えられるが,一番簡単な方法は,より簡単には,年末の在庫量を安全在庫量ではなく,目標在庫量に変更する方法である.しかし,この方法だと目標在庫量の設定に曖昧さが残る.より実用的な方法としてローリングホライズン方式がある.この方法は,12ヶ月の静的な問題を,毎月時間をずらしながら解いていくものである.毎月12ヶ月分の問題を解き直すので,動的な環境の変化にも追従できる.
スケジューリング最適化
工場長の承認も得れたので現場の方に生産計画を提出したところ,生産資源をきちんと考えないと,生産可能かどうか判断できないとの指摘を受けた.
さて,どうすれば良いだろうか?
月次の生産最適化モデルは,タクティカルレベルの意思決定であり,より細かい生産計画はオペレーショナルレベルのスケジューリング最適化で行う必要がある.ここでは,SCMOPTに含まれるスケジューリング最適化システム OptSeq を使って問題を解決することにしよう.
OptSeqは様々な付加条件に対応できるが,ここでは簡単のため単一の資源制約のもとで,スケジューリング最適化をしてみる.結果は,以下のような詳細なガントチャートが得られる.もちろん,上述のローリングホライズン方式を用いて,適当な期間ごとに再最適化を行い,スケジュールを見直す必要がある.
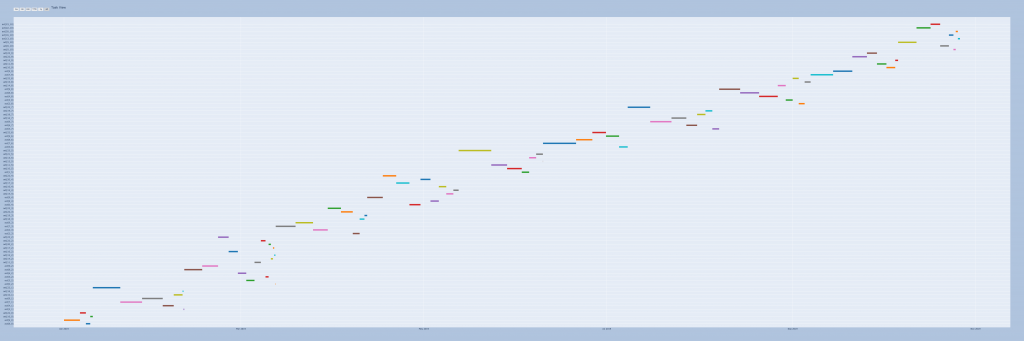
本ケーススタディで使用したのはロットサイズ最適化システム OptLot とスケジューリング最適化ソルバー OptSeqです.両方とも,サプライ・チェイン最適化システムSCMOPT に含まれています.
SCMOPTデモ&トライアルはこちら