在庫最適化(ケーススタディ4)
注意:このケーススタディは,幾つかの企業のコンサルティングから抽出したもので,特定の企業を想定したものではない.データや登場人物は,架空のものである.
社内で新しい倉庫の立地について検討したところ,営業部と倉庫の担当者から在庫が考慮されていないのではないかと問われた. さて,あなたは次に何をすれば良いのだろうか?
SCMOPTのサプライチェイン基本分析システム SCBASには,基本的な在庫解析が含まれているので,まずはそれを使ってみよう.
リスク共同管理分析
リスク共同管理分析は,在庫をサプライ・チェインの上流(工場側)に置くべきか,下流(顧客側)に置くべきかの簡易判断をしてくれる.この会社の場合は(需要をランダムに同じ分布で生成したので当然だが),需要の相関が強いため,上流に置いてもあまり在庫の削減はできないことが分かる.需要が無相関だと,顧客数を nとしたとき 「nの平方根分の1」になることが知られているが,この場合はほとんど削減されない.
在庫基本分析
次にSCBASの在庫分析関数で,(工場が1つと仮定した場合の)工場における生産ロットサイズや安全在庫量を計算する.これは,古典的な経済発注量モデルと新聞売り子モデルを用いたものである.これによって,製品別の需要量,標準偏差,在庫費用,ロットサイズ,安全在庫量などが計算される.
安全在庫配置
次に,安全在庫配置システム MESSA (MEta Safety Stock Allocation system)を利用して,ネットワーク全体での在庫の配置を最適化する.
準備として,ロジスティックネットワーク設計モデルで得られた最適フローをもとに,集約された顧客(クラスター),倉庫,工場ごとの(1日あたりの)製品の需要の平均と標準偏差を計算する.
これが,安全在庫配置を最適化するための基本データとなる. このモデルで決めるのは,在庫保管地点ごとの保証リード時間(サービス時間)である.
このモデルでは,製品ごとに在庫補充の流れを表すネットワークを構築する.
今回の例では,各製品の在庫は必ず1つの地点から補充されているので,地点における作業時間にリード時間を加えておく.(この仮定は必ずしも成立するとは限らない.ロジスティックネットワーク設計モデルで単一ソース制約を付加しても,工場の容量制約があれば,倉庫は2つの工場から補充を受ける可能性がある.
その場合には,工場と倉庫間に輸送を表す点を追加し,その作業時間を工場・倉庫間のリード時間と設定する.)他にも,在庫費用や品切れ費用を準備する必要がある.在庫費用は評価しにくいデータであるが,ここでは製品の価値と在庫保管率を元に計算することにする.製品の価値は地点別に計算されていると仮定する.ここでは,工場,倉庫,顧客における価値が徐々に増加するように設定しておく.
品切れ(バックオーダー)費用は,製品の価値と同じと考える.つまり,品切れしている場合は製品の価値と同等額が失われたものと考える.在庫費用は,製品の価値に在庫保管比率を乗じたものとする. ここで保管費率は以下の量の和である.
- 利子率(投資額利率)
- 保険料率: 製品の種類および企業の方針によって異なる.
- 消耗費率および陳腐化率: 製品の腐敗,破損,目減りなどを考慮して計算
- 税率: 在庫に課せられる法的な税率(日本では0)
サービス率は品切れを起こさない確率であり,古典的な新聞売り子モデルから,品切れ費用と在庫費用から(つまり保管比率から)計算できる.
安全在庫係数は,需要の分布が決まればサービス率から計算できる.ここでは.需要は正規分布と仮定して計算する.(顧客の需要は正規分布とは限らないが,クラスターに集約された顧客や倉庫,工場に集約された需要は正規分布に近いと考えられる.)在庫保管地点のデータと,地点間の情報を保管した部品展開表(BOM)データを元に,安全在庫配置最適化を行う.
工場と倉庫での製品の価値が同等と仮定した場合,以下のような結果が得られる. 点の大きさが正味補充時間(安全在庫を保持する日数)を,点の色の濃さが保証リード時間を表している この場合は,工場には在庫を置かず倉庫にまとめるのが最適であることが分かる.工場の保証リード時間は長く,倉庫が発注をしてから生産を開始するため在庫はなしで運用する. そのかわり,倉庫には20日分程度の在庫を保持する.
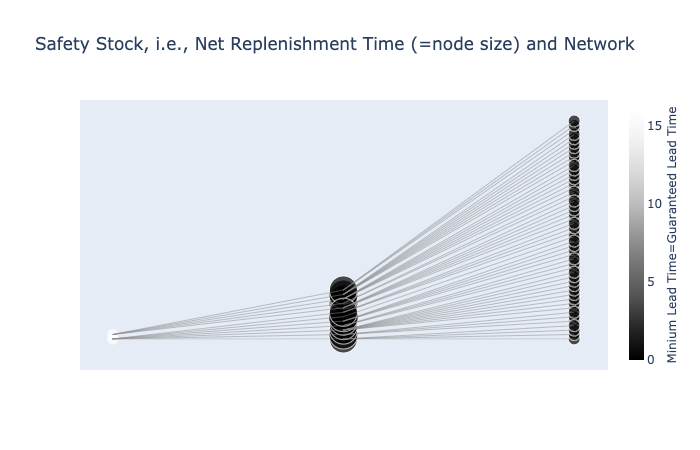
倉庫における製品の価値が工場での価値の2倍と仮定した場合は,以下のような結果が得られる.この場合は,すべての地点の保証リード時間が0となり,すべての地点で自分の作業時間分の安全在庫をもつのが最適になる.
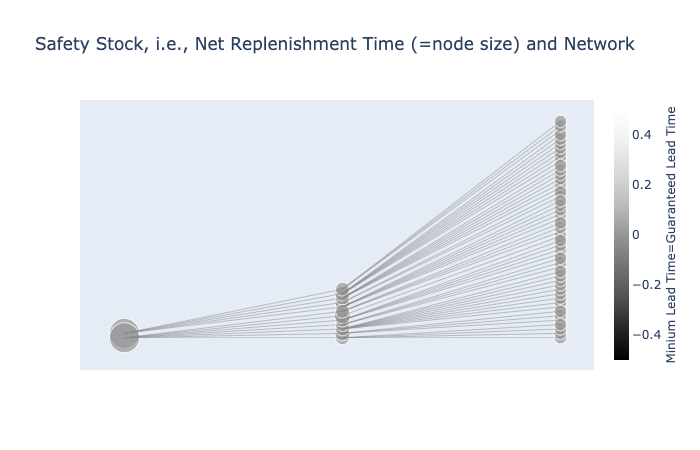
基在庫レベル最適化
安全在庫配置システムMESSAには,シミュレーションをしながら基在庫レベルを最適化するための方法も入っている.この手法は,各地点での1日あたりの処理量上限の制約も付加できるが,ここでは十分な処理能力があると仮定して,最適化を行う.
この手法では在庫がない場合に,下流の地点の注文をどのように配分するかを定義する必要がある.ここでは,ロジスティックネットワーク設計での製品のフロー量をもとに(実績量をもとに)配分を行うものとする.
各在庫保管地点での在庫の変化の図と最適な基在庫レベルが得られる.1つの顧客と倉庫ならびに工場でのシミュレーション結果の一部を表示する.
基在庫レベルを用いた在庫の運用は簡単であり,各地点の在庫ポジション(在庫量にすでに発注済みで未到着の量を加え,バックオーダー量を減じた量)が基在庫レベルになるように発注するだけである.

本ケーススタディで使用したのはサプライ・チェイン基本分析システム SCBASと安全在庫配置システム MESSA は,サプライ・チェイン最適化システムSCMOPT に含まれています.
SCMOPTデモ&トライアルはこちら